В название статьи вынесена немного измененная фраза из нетленного произведения «Двенадцать стульев», мною горячо любимого и постоянно перечитываемого. Давайте же вместе разберемся, откуда (примерно) берется себестоимость модели. Я не пытаюсь считать чужие деньги, да еще и в чужом кармане, нас интересует чисто техническая сторона вопроса. Итак, основных способов производства пресс-формы два: электроэрозионный и гальванопластика. Разница огромна, но для уменьшения стоимости производители частенько их умело объединяют, и для неопытного взгляда различия будут незаметны.
При первом способе все детали модели проектируются – создается их объемная 3-D модель. Затем для проверки, оператор виртуально собирает детали в модель, и если все хорошо, то проектируются литники (рамки) с учетом расположения питателей (отверстия, через которые в пресс-форму впрыскивается полистирол) и толкатели (небольшие штыри, выталкивающие рамку после разнимания пресс-формы). Через трехкоординатный фрезерный станок, спроектированные пуансон и матрица переносятся на медный электрод, который под большим напряжением в несколько тысяч вольт выжигает в стальной плите детали пресс-формы. Для уменьшения искрения все это происходит в ванной с керосином. Затем фрезеруется литник вместе с толкателями и питателями. Такая пресс-форма имеет очень большой производственный ресурс но и стоит недешево.
Второй способ кажется более простым, хотя первое впечатление обманчиво. Здесь множество подводных камней. Суть способа заключается в изготовлении вручную мастер-модели и последующем ее копировании в гальванической ванне. При этом способе качество полученной модели целиком и полностью лежит на макетчике (человеке с очень умелыми руками) и укладчиках деталей – их ошибки и просчеты исправить будет или невозможно, или очень сложно. Отдельные детали выкладываются в рамки литников с учетом размещения толкателей и питателей и располагаются в гальванической ванне. За неделю или две (зависит от ситуации) на заготовке рамки нарастает металлическая «корка» толщиной до 1мм. После извлечения из гальваники, этот отпечаток по определенной технологии цементируется либо в стальную обойму, либо в обойму из какого-либо другого более мягкого материала – и в этом так же большая разница. В стальной обойме пресс-форма живет дольше, но и технология цементирования гальванического отпечатка сложнее и дороже.
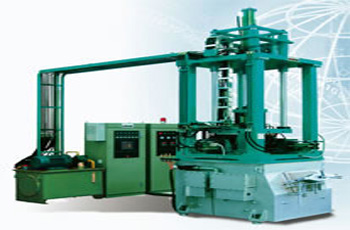 | 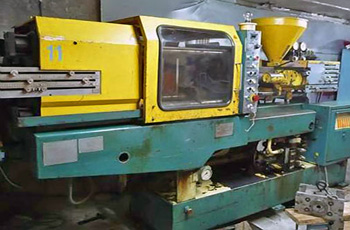 |
Можно, в конце концов, просто залить этот отпечаток эпоксидной смолой с наполнителем в виде специальной дроби, но такая пресс-форма вряд ли выдержит больше тысячи отпечатков, при этом пластик в нее подается по центральному питателю под низким давлением и маленькой скоростью впрыска (отсюда название технологии). По рассказам все очень гладко, но на деле каждый этап содержит большое количество сложных моментов. Нужно создать правильный и точный (с учетом допусков) «мастер», который не расслоится в гальванической ванне. При наращивании «корки» в ванне, не должен пропадать ток (при перебоях внутри отпечатка образуются полости), не должны оставаться полости и трещины в обойме, иначе полистирол под большим давлением просто разорвет «корку» в пласт-автомате, и т.д.
Теперь попробуем посчитать виртуальные деньги, назовем их «кредиты». Пусть стальная пресс-форма стоит 100 000 кредитов (для ровного счета), тогда аналогичная, но рассчитанная на литье под низким давлением будет стоить 10 000 кредитов. Стальная выдержит 100 000 отливок с капитальным ремонтом на 70-80 тысячах. Амортизация пресс-формы (стоимость формы на одну отливку) 100 000 кредитов/100 000 отливок = 1 кредит нужно заложить в себестоимость одного жима пресс формы. Форма для литья под низким давлением выдержит 1 000 отливок. 10 000 кредитов/1 000 отливок = 10 кредитов только амортизации. Вывод – пресс-формы под низким давлением стоят дешевле, но отливки обходятся дороже.
Корпуса больших моделей фирмы А-модел и Моделсвит выполнены по особой технологии. Корпусные детали выкладываются и выклеиваются в матрице нанесением на несколько слоев стеклоткани полиэфирной смолы, цена которой определяется за грамм. Две половинки формы смыкаются под давлением, детали высыхают, после чего форма размыкается. Качество напрямую зависит от материала и квалификации рабочего. Это штучная, ручная работа, а не литье. Затем половинки корпуса или крыльев склеиваются между собой для прочности той же смолой. Корпуса моделей
АН-124 «Руслан» и
Ту-144 фирмы Моделсвит отлиты из полиэфирной смолы, а Amodel - из эпоксидной. Представьте цену сами.
Пока мы считали только амортизацию для пластиковых литников. Нужно добавить стоимость полистирола и стоимость литья, разработку и печать декали (наклейки), инструкции и коробки. Украинские производители, как правило, используют полистирол импортного производства высокого качества, а не «вторичку». Но в любом коммерческом предприятии должна быть заложена прибыль…
Вывод прост – известную и знаменитую модель выпускают большим тиражом в хорошем качестве, благодаря этому цена на неё доступна. Но история авиации пестрит огромным количеством мало серийных машин, известных большей частью специалистам. Модели очень больших самолетов, не пользуются популярностью ввиду сложности хранения коробки и тем более готовой модели. Их выпускают маленькими сериями, превращая владельцев в счастливых обладателей эксклюзивных наборов. Цена на которые (изначально немалая), с каждым годом только растет.